Nitrile Butadiene Rubber (NBR) O-Ring is a type of seal made with Nitrile Rubber material, which is known for its excellent oil, abrasion, and heat resistance, and thus is widely used in many industrial applications. In addition, it also has good water resistance, air tightness and excellent bonding properties. Widely used in the production of a variety of oil-resistant rubber products, a variety of oil-resistant gaskets, gaskets, casing, flexible packaging, flexible hose, printing and dyeing rubber rollers, cable rubber materials, etc., in the automotive, aerospace, petroleum, photocopying, etc., to become indispensable elastic material industry.
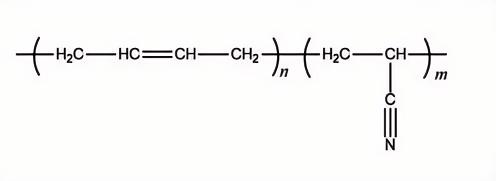
What is the NBR O-rings Material Properties ?
- Oil Resistance: Butyral rubber has excellent resistance to petroleum-based oils, lubricants and fuel oils, making it ideal for oil-resistant seals.
- Abrasion resistance: Butyral rubber has good abrasion resistance and is suitable for use in environments with high friction and wear.
- Heat Resistance: NBR is able to maintain its performance within a certain temperature range, usually ranging from -40°C to +120°C, with some specially formulated NBR being able to withstand higher temperatures.
- Chemical resistance: NBR is resistant to a wide range of chemicals, but is less resistant to certain polar solvents and strong oxidizing agents.
- Mechanical properties: NBR has good elasticity and resistance to compression permanent deformation, but its weather resistance and ozone resistance are not as good as some other rubber materials.
Basic performance characteristics
- Temp:-40℃ to 120℃
- Color:Black or follow RAL Color customsized
- Shore:30shore to 90shore
- Special Materials:FDA, UL, AED and Mil Spec
Acrylonitrile content in NBR (%)
- Very high NBR: ACN content 43% or more
- High NBR: 36%-42% ACN content
- Medium-high NBR: 31%-35% ACN content
- Medium NBR: 25%-30% ACN content
- Low Buna-N: ACN content below 24%
The effect of ACN content on performance
Acrylonitrile rubber in the acrylonitrile content (%) of 42 ~ 46, 36 ~ 41, 31 ~ 35, 25 ~ 30, 18 ~ 24 and so on five, with the increase of ACN content of NBR polarity enhancement, the chain flexibility decreases, the inter-chain interaction force increases, the molecular chain of the double-bond content decreases, the degree of saturation increases, which also caused a series of changes in performance, its oil resistance, airtightness and abrasion resistance. The oil resistance, air tightness and abrasion resistance increase, while the processability and cold resistance decrease.
Which are the NBR O-rings Applications ?
Butyral O-rings are widely used in automobile, aviation, oil and gas, chemical industry, machinery manufacturing and other industries for sealing oil pipes, hydraulic systems, fuel systems, braking systems, etc.
How does NBR O-rings Manufacturing Process ?
NBR O-Rings are usually manufactured by molding or extruding process. Molding is to put the pre-mixed NBR material into the mold and form it under high temperature and high pressure; extruding is to extrude the NBR material into the shape of O-Ring through the extruder and then vulcanize it.
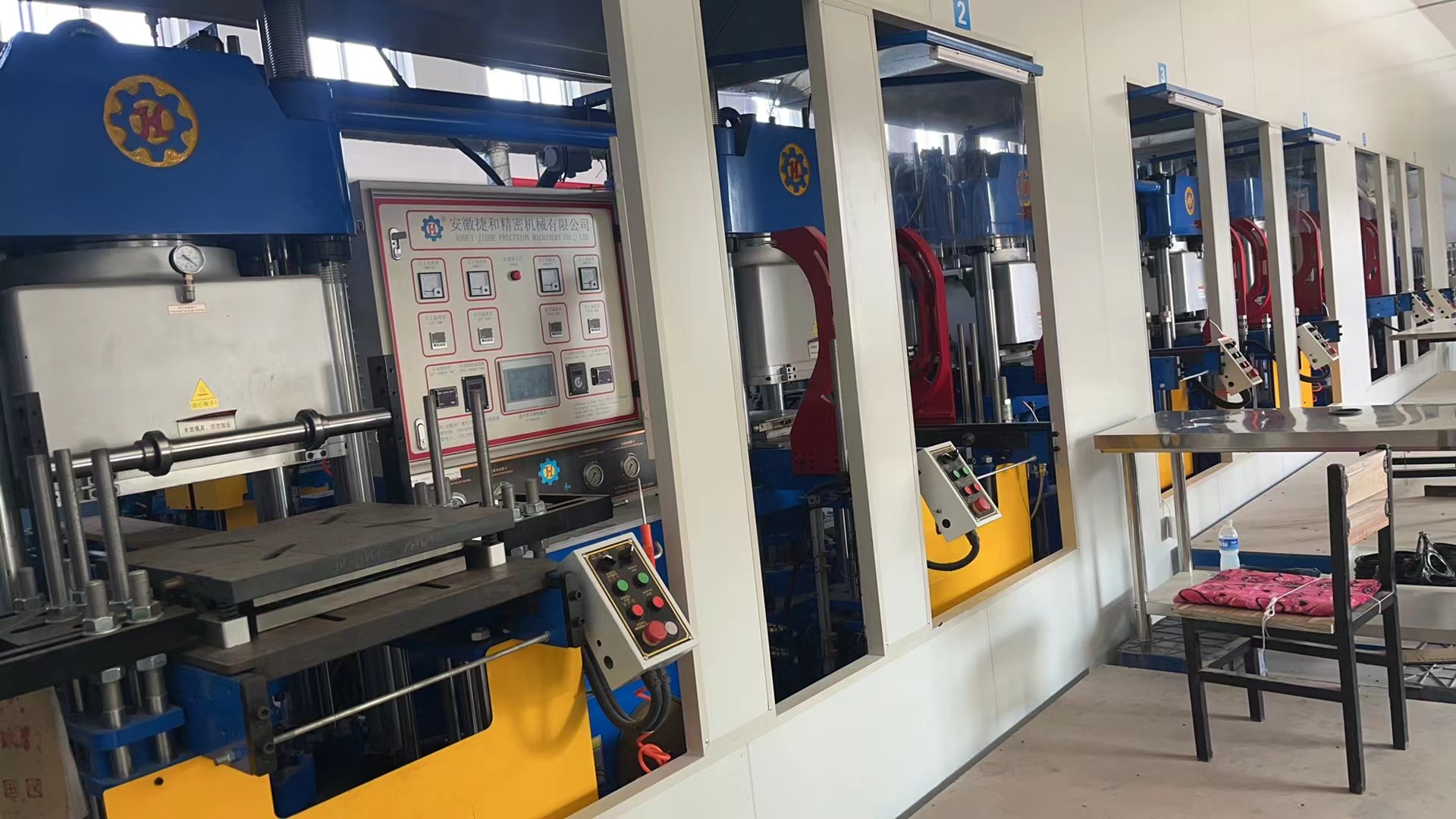
NBR O-rings Specifications and Standards ?
- AS 568 Standard Size
- JIS B2401 Standard Size
- BS ISO3601-1 Standard Size
- BS 4518 Standard Size
- GB 3452 Standard Size
- Customized non-standard
What should we pay attention to ?
- Storage conditions: NBR materials should be stored in a dry, cool, well-ventilated place, avoiding direct sunlight and high temperatures.
- Use environment: Although NBR is resistant to oil and abrasion, it may be affected in certain polar solvents and strong oxidizer environments.
- Installation Requirements:Avoid scratching or twisting when installing NBR O-rings to ensure sealing effect. The selection and use of NBR O-rings need to be determined according to the specific application environment and requirements to ensure the best sealing effect and service life.